It is generally recognized that Tank cleaning and Gas freeing is the most hazardous period of tanker operations.
This is true whether Washing for clean ballast tanks, Gas freeing for entry, or Gas freeing for Hot work. The additional risk from the Toxic effect of petroleum gas during this period cannot be over-emphasized and must be impressed on all concerned. It is therefore essential that the greatest possible care is exercised in all operations connected with tank cleaning and gas freeing.
The safest way to gas free an oil tank which is fitted with an inert
gas system is to use a fan and vent the tank. Before entry, an O2
meter must be used and the tank must also be checked with an
explosimeter. These meters must also be used while in the tank.
The sketch shows a diagrammatic view of an explosimeter. In
fresh air, the combustion chamber is cleared of any residual gas
by the aspirator bulb. The meter is then switched on and time is
allowed for the detector element to heat up. With the check switch
closed, the zero adjustment of the meter is checked.
In suspect
atmosphere, the aspirator bulb is operated with the check switch
closed, noting the meter reading. If there is gas in the atmosphere,
this will burn in the combustion chamber due to the heating effect
of the element. The burning will cause the temperature of the
element to rise, giving a rise in electrical resistance of the element
as it is proportional to the rise in temperature. This gives a reading
on the meter which is calibrated to read the lower % of lower limit
of explosive concentration of gas.
The O2 meter works on the principle that oxygen is
paramagnetic and that nitrogen is diamagnetic.
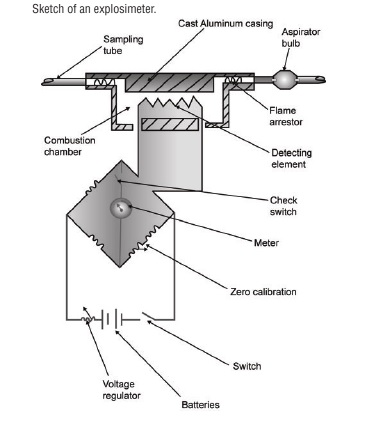
Exposimeter sketch
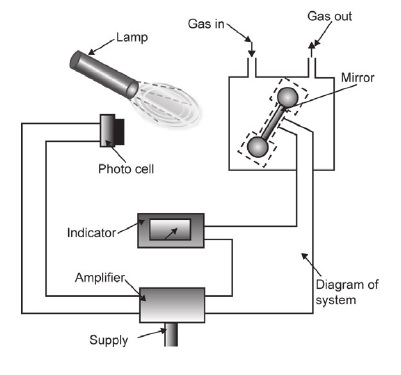
Gas analysing instrument
With reference to the sketch, two small spheres filled with
nitrogen are arranged, dumb bell fashion, on a pivot between
pole pieces. This causes a torque to be applied to the dumb bell.
The gas to be analysed is passed through the pole pieces. The
magnetic field concentrates the oxygen in the gas and a small
force, proportional to the oxygen concentration, exerts a further
torque on the dumb bell arrangement.
The mirror on the dumb bell arrangement reflects light from a
source to a photo cell where it is converted to an electric signal
for input to an amplifier. The amplifier output is arranged to
pass through a small coil around the dumb bell arrangement
and generates a torque which is in opposition to that applied by
the paramagnetic effect.
A current of measured flow is required to provide a balancing
torque and this is proportional to the oxygen concentration.
Before entering the tank, the oxygen content must be 21%.
Refer to ISGOTT regarding the various hazards involved.
Also, follow the check items as described in Tank Cleaning, Purging and Gas Freeing Checklist
Precautions below mentioned shall be considered to Hazard identification and Risk control In due course of a Risk management.
Prevent human injury
The chief officer is the responsible person for such operation and shall brief all crew regarding the safety measures to be followed on deck.
During gas freeing operations only personnel directly involved in the Gas freeing operations should be allowed on the main deck. Tank openings shall be guarded.
The proposed duration and Job / Watch schedule
All crew involved in the Gas freeing operations must wear appropriate clothing.
Antistatic precautions must be observed on deck.
The covers of all tank openings should be kept closed until actual ventilation of the individual tank is about to commence.
If small crafts are alongside the tanker, their personnel should also be notified.
The atmosphere in the operations area should be monitored for explosive hydrocarbon vapors during such conditions.
Atmosphere control for tanks & pipes to be Gas free
During Gas purging / Gas freeing operation, the tank and pipelines atmosphere should be controlled and not allowed to enter the flammable range (of the flammability diagram) at any time.
In all operations, where gas is being vented (purged or gas freed), great vigilance should be exercised, as the highest concentrations of gases (hydrocarbon or inert gas) is emanated at the start of such operations.
Hence, where portable gas free fans are used, where the venting velocity is minimum, great care needs to be exercised.
The venting of flammable gas during Gas freeing should be by the vessels approved method. Where gas freeing involves the escape of gas at deck level or through tank hatch openings the degree of ventilation and number of openings should be controlled to produce an exit velocity sufficient to carry the gas clear of the deck.
Once an oil cargo tank has been confirmed free of explosive hydrocarbon vapors (less than 1% HC LEL), toxic gases, contaminants and the oxygen content is measured at 21.0% the tank should be isolated from the IG (Inert Gas) main line by inserting blind flange at the IG tank supply valve.
IG in adjacent tanks to be reduced to minimum (200mmAq) to prevent the ingress of hydrocarbon gas / IG through any leaking valves, pipelines or (damaged/cracked) bulkheads.
All other valves to the tank (including Machine valves) should be in closed position.
If the tanks are connected by a common venting system, each tank should be isolated to prevent the transfer of gas to or from other tanks.
Prevent for Gas enter into accommodation area
To prevent hydrocarbon vapors to accumulate in the accommodation areas, it may be necessary to change course during Gas freeing operations.
The presence of Sparks / Hot soot emanating from the funnel stacks should be considered.
If gas freeing is taking place while the vessel is at anchor, it may be necessary to suspend operation during periods with calm or no winds (local regulations regarding port permissions / emissions shall be complied with).
Intakes of central air conditioning or mechanical ventilating systems should be adjusted to prevent the entry of petroleum gas, if possible by Partial recirculation of air within the spaces, but should be maintained Positive pressure in accommodation.
If at any time it is suspected that gas is being drawn into the accommodation, central air conditioning and mechanical ventilating systems should be stopped and the intakes covered or closed.
Care for Gas free equipment
Portable fans or blowers should only be used if they are hydraulically, pneumatically, ,water or steam driven. Their construction material should be such that no hazard of incendiary sparking arises if, for any reason, the impeller touches the inside of the casing.
Portable fans, where used, should be placed in such positions and the ventilation openings so arranged that all parts of the tank being ventilated are equally and effectively gas freed. Ventilation outlets (discharged gas) should generally be as remote as possible as possible from the fans.
Portable fans, where used, should be so connected to the deck that an effective electrical bond exists between the fan and the deck.
Where cargo tanks are gas freed by the permanently installed blowers, all connections between the cargo tank system and the blowers should be blanked except when the blowers are in use. (ie blower outlets / inlets)
Before putting such a system into service, the cargo piping system, including crossovers and discharge lines, should be flushed through with sea water and the tanks stripped.
Fixed Gas freeing equipment may be used to gas free more than one tank simultaneously but must not be used for this purpose if the system is being used to ventilate another tank in which washing is in progress.
Precautions for entry after Gas freeing
In addition to follow Procedure or Entry into Enclosed Spaces
, below precautions shall be applied.
On the apparent completion of Gas freeing any tank, a period of about 10 minutes should elapse before taking final gas measurements. This allows relatively stable conditions to develop within the tank space.
Tests should be made at several levels and, where the tank is sub-divided by a wash bulkhead or in oddly shaped tanks, in each compartment of the tank.
In large compartments such tests should be made at widely separate positions.
If satisfactory gas readings are not obtained, ventilation must be resumed.
Regular gas monitoring and checks should be carried out by personnel entering the tank in using personal gas meters. The possibility of vapors build-up due to disturbing of sludge at bottom, due to man entry foot steps and countermeasures for the same is to be evaluated and decided, prior to entry.
Related articles:
General precautions for tankers
Inert gas system
What is toxic releases onboard and associated hazards?
....
Safety precautions prior transferring oil
How to report in case of an oil spillage onboard
Inert condition in tanker
Oil disaster prevention
Tanker equipment and machinery
Pumproom procedure
General guidance for oil tankers
General precautions at work for tankers

Other info pages !
Ships Charterparties Related terms & guideline
Stevedores injury How to prevent injury onboard
Environmental issues How to prevent marine pollution
Cargo & Ballast Handling Safety Guideline
Reefer cargo handling Troubleshoot and countermeasures
DG cargo handling Procedures & Guidelines
Safety in engine room Standard procedures
Questions from user and feedback Read our knowledgebase
Home page

ShipsBusiness.com is merely an informational site about various aspects of ships operation,maintenance procedure,
prevention of pollution and many safety guideline. The procedures explained here are only indicative,
not exhaustive in nature and one must always be guided by practices of good seamanship.
User feedback is
important to update our database. For any comment or suggestions please Contact us
Site Use and Privacy - Read our privacy policy and site use information.
//Home //Terms and conditions of use
Copyright © 2015 www.shipsbusiness.com All rights reserved.
