Many crude oils contain hydrogen sulphide gas in solution, which may be liberated during handling and storage. The gas is formed by the decomposition of sulphur compounds in the crude and is highly toxic and corrosive.
H2S can also evolve from mixtures of saltwater, oils sewage and chemicals containing sulphur. Therefore it must be remembered that there are other possible sources of H2S other than from cargo loaded or residues from previous cargoes.
The gas concentration in raw crude is often reduced to an acceptable level by a stripping process prior to shipment. Even after stripping, however, the gas content may still be sufficiently high to be dangerous to the personnel if reasonable safety precautions are not followed.
Hydrogen sulphide gas is colourless, transparent and is commonly recognised by its characteristic smell of rotten eggs. However absolutely no reliance is to be placed upon this method of detection as H2S deadens the sense of smell very quickly. Dangerous concentrations may be present that cannot be detected by smell alone.
Precautions must be taken to prevent exposure of personnel to H2S gas. Reference is to be made to other parts of this section and to ISGOTT.
There is growing evidence to suggest that H2S levels in cargoes are on the increase. Among the crude oils most commonly carried which contain hydrogen sulphide are listed below, however it must be remembered that any cargo or cargo residue may contain H2S.
Masters must also be aware that strict regulations exist in some loading ports regarding the expelling of petroleum vapour containing H2S concentrations in excess of 5-10 ppm in air. Some countries, particularly in Europe, have already stipulated maximum H2S levels in tanks prior to loading and some terminal operators have reduced their maximum arrival levels from 10ppm to 5 ppm. Masters are to ensure that they are aware of any such regulation well in advance of arrival in case they have to remove concentrations of H2S by purging or cleaning.
The gas concentrations within these crudes and other crudes containing hydrogen sulphide in solution may vary from time to time. In the absence of specific information from the loading terminal they must always be regarded as being potentially dangerous.
The Company provides equipment to monitor levels of H2S on board in the form of a portable H2S meter together with a Draeger Multigas Detector and tubes for H2S.
H2S -Threshold Limit Value (T.L.V.) and General Precautions
The TLV-TWA for H2S is given as 5 ppm but concentrations in enclosed spaces are to be reduced as far as possible below this level and if men are to work in the space without breathing apparatus, a nil concentration must be achieved before entry is permitted and effective ventilation must be maintained.
The following guide, with the effects under various atmospheric concentrations on exposed persons, gives an indication of the dangers involved:
Measured In Air by Volume
50 - 100ppm Eye and respiratory tract after exposure of 1 hour.
200 - 300ppm Marked eye and respiratory tract irritation after exposure of 1 hour.
500 - 700ppm
Dizziness, headache, nausea etc within 15 minutes, loss of consciousness and possible death after 30 - 60 minutes exposure.
700 - 900ppm Rapidly produces loss of consciousness and death after a few minutes.
1000 - 2000ppm Instantaneous death. Apparent death from H2S is not irreversible as prompt and efficient artificial respiration may restore life.
It is important to realise that the concentration of gas can be measured and expressed in two different ways:
Parts per million - in the liquid, by weight.
Parts per million - in the air, by volume.
There can be a vast difference between the two measures. The measure in air will be higher and can be a great deal higher. For example, chemists have measured a concentration of 700 ppm (deadly) in the vapour stream coming from an ullage opening when a tank was being "topped-off" with crude containing only 70 ppm of hydrogen sulphide in the liquid.
It is important to ascertain which method of measurement is being used. Producers and processors frequently use the liquid measure.
Masters are to endeavour to ascertain from the terminals the H2S content of cargoes being loaded. When handling a cargo with noticeable or known hydrogen sulphide content or when ballasting after discharge of such a cargo the following precautions are to be followed:
- The officer supervising the operations must keep a sharp watch on personnel for signs of fatigue or distress.
- Lifelines, breathing apparatus and resuscitator must be readily available.
- Loading through the pumproom must be avoided where possible to reduce the possibility of H2S contamination of the pumproom atmosphere.
- Gas must be vented through the tank venting system and, if ullage opening is necessary, the ullage plugs should be kept open for the least possible period of time.
- When ullaging tanks, personnel are to work in pairs and stand at right angles to the wind direction in relation to the ullage opening.
- Before entering a pumproom the mechanical ventilation system is to be started and the atmosphere therein is to be tested for dangerous concentrations of gas. If the pumproom has to be entered under such circumstances the full Enclosed Spaces Entry Procedure must be carried out and an Action Plan completed.
- Other spaces into which H2S may have been drawn should be ventilated and the atmosphere checked before entry.
- Persons overcome by H2S are to be moved to a gas free area immediately and artificial respiration is to be administered at once using the Resuscipac initially if available. Oxygen is to be administered and medical advice sought.
Gas tests must be made on deck and in the accommodation and machinery spaces at regular intervals and particularly during "topping-off" operations. If concentrations of 10ppm and above are recorded inside the accommodation, or 50ppm on deck more than 3 metres from a gas outlet, the loading rate must be reduced and if this does not result in a decrease of the gas concentration loading must be stopped until conditions have improved.
- During discharge the pumproom bilge’s are to be kept as dry as possible. Any small leaks must be stopped and not left to build up in the bilges. If necessary and as a last resort consideration should be given to transferring the bilges to the slop tanks.
- During loading or ballasting operations, conspicuous notices warning of the potential danger from H2S gas must be posted on deck at pumproom entrances, and at the entrance to any other space which could be affected.
Where it is expected that H2S levels in a cargo are likely to exceed 100ppm in air a full risk assessment must be carried out. All precautions are to be followed for loading and then after loading samples of the vapour spaces must be taken in order to measure the H2S content. If the result is less than 100ppm no further action is required however H2S levels should continue to be monitored and recorded on a daily basis. If the result is greater than 100ppm the vessel is to strictly follow additional safety procedures for carriage and discharge.
Precautions Required Prior to and During Loading High H2S Crude Oil Cargoes
Procedures to be Adopted During the Carriage of High H2S Cargoes
a) Whilst the vessel is on passage, a careful watch on tank pressure must be maintained throughout. A log is to be maintained of tank pressure(s), air temperature, atmospheric pressure and weather. This will assist in identifying pressure characteristics of cargo.
If cargo or vapour leakage is identified or suspected, the cargo area is to be evacuated immediately and the Officer of the Watch informed. Deck apertures, where leakage may occur (tank lids, purge pipes, valve glands etc) should be monitored on a regular basis.
b) During the heat of the day, pressure will rise as the tank’s atmosphere heats up. Pressure may be allowed to rise to 90% of the relief valve setting before venting takes place. There may be a reluctance to hold onto the gas and a tendency to relieve the pressure at too low a level. However, holding on to gas pressure will, on most occasions, ensure that the introduction of inert gas later in the day, as the atmosphere cools, will not be required. If venting is necessary then it is preferable that it is carried out in daylight, during scheduled breaks in the normal working day. Cooling of deck by water to control pressure should be considered.
c) Should the pressure rise to greater than the 90% value, and therefore require venting, the following procedures must be adopted:
i. It is essential that the accommodation is kept under positive pressure to prevent the entry of Hydrocarbon Vapours – the operation of sanitary and galley extraction fans will cause a vacuum and therefore the air conditioning system intakes must not be kept fully closed. The accommodation air conditioning system should be maintained on partial re-circulation during cargo operation.
ii. All external doors and vent flaps are to be confirmed closed.
iii. Vessel’s anemometer checked and true wind direction in the vicinity of vapour emissions determined.
iv. PA announcement to be made advising that cargo tanks are about to be vented and all personnel to remain inside the accommodation or engine room control room as appropriate.
v. The operator of the Inert Gas (IG) mast riser valve, if locally operated, must wear Compressed Air Breathing Apparatus (CABA), during venting operations. Where possible, during venting the valve operator should position himself to windward of the gas stream.
vi. The Officer of the Watch (OOWOfficer of the Watch), both on the bridge and in the engine control room (ECR) must be informed in advance.
vii. The bridge is to be adequately manned and equipped with an Emergency Life Support Apparatus (ELSA) set and personal monitor.
viii. Engine room manning should be reduced to the minimum level consistent with safe operations. All other personnel are to gather inside the accommodation. The personnel lift is not to be used during venting operations.
ix. Prior to giving permission for the riser valve to be opened the OOWOfficer of the Watch is to confirm that all personnel are inside the accommodation or engine room control room as appropriate.
x. The pressure should be reduced by the minimum required, bearing in mind time of day, temperature, and vessel movement and in line with the gas generation experience on that particular voyage. The IG pressure should be periodically recorded to allow predictive venting to take place.
xi. The vessel’s heading should be adjusted such that any gas emission from the mast riser is carried away from the vessel. Speed and /or course may need to be adjusted to ensure that this does occur.
xii. If the vessel is proceeding into congested waters where course alterations would be difficult, it would be prudent to release most of the pressure before that time. If it is necessary to release pressure where manoeuvring is not possible and relative wind direction is from ahead, than it must be released in short bursts at high velocity in order to carry the gas as high as possible away from the vessel.
xiii. On completion of venting operations the CABA wearer must carry out a full check of the external accommodation and deck areas to ensure that no residual pockets of H2S gas remain.
xiv. Once the area has been declared safe a PA announcement is to be made to advise all personnel that venting is complete and the area is safe.
Additional Precautions on Passage
a) Pump room entry to be restricted to essential requirements only and atmosphere to be tested for oxygen, hydrocarbons and H2S, on each occasion prior to entry.
b) Entry into confined spaces is to be minimised during the loading passage.
c) To minimise the risk of exposure, cargo sampling and temperature readings should not be taken whilst on passage.
d) For any emergency situation involving cargo leakage or a release of vapour all personnel are to muster inside the accommodation. Those involved in repair work or spill cleanup must wear CABA.
e) There shall be no work aloft carried out other than that directly related to the operational safety or navigation of the vessel.
f) Whilst on passage the IG line abaft the deck seal is to be tested for the presence of H2S on a daily basis.
g) No routine planned maintenance, which may affect the system integrity, is to be carried out on the vessel’s IG system during the loaded passage.
h) Pressure testing of cargo-related equipment is not to be carried out during the loaded passage. If the crude oil wash line is to be pressure tested then this operation is, so far as possible, to be carried out using a non H2S crude.
i) In the event that internal cargo transfer is to be carried out on passage then a full risk assessment must be carried out.
j) Only essential maintenance is to be carried out on cargo-related equipment.
k) Where possible planning should enable routine planned maintenance of safety systems to be carried out prior loading.
l) Compressed air cylinders are not to be recharged on loaded passage unless carried out under control which addresses the air quality at the compressor.
All new joining personnel onboard are to be made aware of the hazardous nature of the cargo and details of the approved procedures that have been implemented.
Precautions Required for Discharging High H2S Crude Oil Cargoes
a) All applicable procedures defined in the documents relating to the Loading and Carriage of high H2S cargoes and are to remain in force during the discharge operation.
b) Prior to arrival at the discharge port the vessel’s containment system must be checked to confirm that there are no cargo or vapour leaks. If cargo or vapour leakage is identified or suspected the cargo area is to be evacuated immediately and the Officer of the Watch informed. Particular attention must be paid to cargo tank lids, purge pipes, valve glands etc. Any repairs that are necessary shall be carried out by personnel wearing Compressed Air Breathing Apparatus (CABA) equipment.
c) Vessel’s contingency plans should be reviewed and amended as necessary taking into account of experiences during loading and carriage of the cargo. Part of the plan must consider the medical aspect of the effects of exposure to H2S. Plans must include the requirements that members of fire party wear Compressed Air Breathing Apparatus (CABA) on all occasions where toxic vapours may exist. Additional points to be considered include medical treatment and considerations, muster stations, lifeboat preparations and use of Personal Protective Equipment
d) The relevant Marine Safety Data Sheets (MSDS) for the cargo is to be posted.
e) Within the discharge plan, the Health and Safety aspect of discharging the high H2S cargo must be addressed. All aspects of these instructions, in particular those relating to gas venting, are to be discussed and agreed with shore officials prior to commencing discharge. A pre-discharge Safety Meeting is to be held with all crew.
f) Prior to arrival at the discharge port the vessel will reduce the cargo tank pressure to the lowest acceptable level in order to reduce the possibility of having to vent tanks whilst at the berth.
g) Consideration should be given to reducing the setting of Inert Gas (IG) pressure controller during discharge. The agreed setting must be incorporated into the cargo discharge plan.
h) Access to the vessel is to be restricted to persons on legitimate ship’s business.
i) Whilst in port, the activities of shore personnel are to be closely controlled and must be in line with the vessel’s agreed procedures. Particular attention must be paid to these procedures during venting, connection, disconnection and sampling/measuring.
j) Storing and port formalities are to be completed in a controlled manner.
k) New joining personnel must, on joining, be immediately appraised of the health and safety aspects and precautions that are in place regarding the high H2S cargo onboard.
l) During discharge operations, access to the accommodation is to be restricted to one entry point only and this should be agreed prior to the vessel’s arrival at the load port. All other doors and ports should remain closed throughout the discharge operation.
m) It is essential that the accommodation is kept under positive pressure to prevent the entry of Hydrocarbon Vapours – the operation of sanitary and galley extraction fans will cause a vacuum and therefore the air conditioning system intakes must not be kept fully closed. The accommodation air conditioning system should be maintained on partial re-circulation during cargo operation.
n) Prior to berthing and commencement of discharge, a PA announcement must be made to remind all onboard of the hazardous nature of the cargo and advise that additional precautions are to be enforced.
o) At all times during the discharge operations only minimum personnel are to be permitted outside the accommodation and it is recommended that this be limited to those directly involved in the cargo operation. Personal H2S meters should be worn as required by ISGOTT.
p) Engine room manning should be kept to a minimum during the discharge operation. When working outside the Engine Control Room (ECR), engine room personnel are to carry portable UHF radios. Prior to cargo tank venting taking place, engine room personnel must be advised and throughout the vending period, they must remain within the accommodation block or engine control room.
q) If crude oil washing is to be undertaken then the sections of line in use should be minimised and at all times be limited to those machines in use. All branches and legs are to be drained down immediately after use as far as practical.
r) Prior to crude oil washing (COW) operations the oxygen levels in the cargo tanks must be measured. The individual measuring the tanks must be wearing CABA and equipped with another H2S monitor. Readings should be limited to one per tank and full venting precautions are to be implemented during the measurement period.
s) Where possible the mast riser valve should be kept shut during discharge and no cargo tank venting should take place. However, should it become necessary to vent, the cargo area must be evacuated and all personnel must remain inside the accommodation or engine control room until venting has been completed. Prior to resuming normal activities on deck, sufficient time must be allowed for any residual gas in the cargo area to disperse.
t) Where venting is to take place, the following procedure is to be adopted:-
Wind conditions to be assessed to confirm that adequate gas dispersion, clear of the vessel’s accommodation, can be achieved.
- Shore representatives are to be given advanced notice of the vessel’s intention to vent cargo tanks. Any workboats in the vicinity of the vessel should also be advised.
- A PA announcement is to be made, advising all onboard that cargo tank venting is about to take place.
- The operator of the IG mast riser valve, if locally operated, must wear Compressed Air Breathing Apparatus (CABA) during venting operations. Where possible, during venting the valve operator should position himself to windward of the gas stream.
- Venting should not commence until it has been confirmed that all personnel are inside the accommodation or engine control room, as appropriate. The personnel lift is not to be used during venting operations.
- If vessel is at an (Single Buoy Mooring) SBM and a tug is available then tug may be used to pull the vessel across the wind to assist with dispersion.
- Venting should be minimised and is recommended that the vapour is released in short, high velocity bursts to maximise dispersion rates
- On completion of venting operations the BA wearer should carry out a full check of the cargo tank deck area and external accommodation areas to ensure that no residual pockets of H2S gas remain.
- Prior to each entry to the pump room, checks are to carried out for oxygen, hydrocarbon and toxic gas. As per agreed procedures, persons entering pump room are to carry escape set and personal gas detection meter. Pumproom ventilation is to be verified as operating to the designed standard.
- Exhaust fans, where fitted, to be running at least 30 minutes prior to entry to the following areas: foc’sle space, storerooms, steering flat and other such spaces. Fans should not be operated unless the deck atmosphere is free of H2S.
- When necessary to move portable tank gauging equipment from tank to tank, CABA must be worn. In addition, CBA must be worn by those directly involved in the pre and post discharge cargo tank survey. Cargo tank pressure must be reduced to minimum and full venting precautions must be implemented for the duration of this operation.
- If H2S is detected in high concentrations, or if there is any doubt as to the presence of H2S, then discharge must be stopped immediately and the cargo area evacuated.
- No non-essential maintenance is to be carried out on safety systems whilst discharging this cargo.
- Recharging of compressed air cylinders during discharge is not to be carried out except under control which addresses the issue of air quality at the compressor.
In the event of an incident refer to the shipboard Oil Pollution and Emergency Plan (SOPEP).
Emergency Procedures For Toxic Vapor Release on Tankers or accidental Chemical Spill on Containerships
The procedures mentioned below are guidelines in event of an accidental Toxic Vapor Release on Tankers and for an accidental Chemical Spill on Containerships.
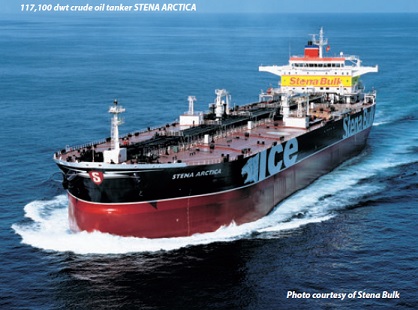
Fig: 117,100 dwt crude oil tanker STENA ARCTICA
In Case Of Tankers:
Raise alarm
If in port, advise terminal
Stop any Cargo Operations and then Shut Tank and Manifold Gate Valves
All crew to muster inside accommodation and close all doors
Stop air conditioning / ventilation to living and working spaces.
(But maintain to operate the Pump Room Exhaust Fans, if applicable)
Notify nearest coast state and other vessels in vicinity
If at sea, Master to alter course, if possible, to blow vapors away from accommodation
Check MSDS for emergency procedures
Crew, wearing SCBA and PPE, go about to isolate source of leak.
In Case Of Container ships:
Raise alarm
Identify the cargo involved in the spill – if it is IMDG cargo, then from corresponding UN number, the specific EmS (“Emergency schedule for Spillage and Fire” in IMDG Supplement) is to be noted.
If not, it can be washed overboard if vessel is not in a special area or less than 12 miles from coast.
Refer to the appropriate EmS Spillage Schedule of spilt cargo for general guidance and measures for spill on deck and under deck.
Consider sealing off ventilation, air conditioning and other openings to living and working spaces.
If necessary, seek expert advice from shore
If the chemical in the spill is harmful to skin or if in least doubt, chemical suit to be worn by persons tackling the spill
If the spill is inside a confined space, SCBA is to be used.
If the cargo is a marine pollutant, it is to be collected onboard and discharged ashore. Any pollution to be reported as per SOPEP.
Any contaminated clothing to be discarded
First aid to be administered if required, as per MFAG
(“Medical First Aid Guide” in IMDG Supplement)
Related Information
General guidance for oil tankers
Tanker equipment and machinery
Pumproom procedure
General precautions prior entering freezing areas
Ship to ship transfer arrangement
Pumproom inspection for tankers
Safety precaution during oil handling operations
Treatment for waste oil or oily bilges
Oil pollution prevention method
General precautions for tankers
Tanker equipment and machinery
General guidance for oil tankers
Crude oil washing for tankers
Oil tanker handling more opeartional guideline
Oil pollution control method
Gas freeing arrangement for oil tanker
Handling guideline for oil cargo
Oil pollution prevention method
Preparation for loading oil cargo
How to prevent spillage of oil cargo
General precautions for oil cargo loading in tankers
General precautions for tankers
General guidances for tank cleaning
General precautions for ballasting procedure
Tanker operation in a laden voyage
Preparation for discharging oil cargo
General precautions for oil cargo discharging
How to ensure safe working area onboard oil tankers
Shipping industry recognizes environmental protection as one of its highest priorities and that every effort should be made to conserve and protect the environment from marine, atmospheric and other forms of pollution.
Our articles are based on various shipboard activities,prevention of pollution,safe operation & maintenance procedure. We welcome any feedback from our visitors.
For any comments or suggestions please Contact us
Site Use and Privacy - Read our privacy policy and site use information.
Terms and conditions of use
Copyright © 2010 www.shipsbusiness.com All rights reserved.
|
Ships business.com
Shipsbusiness.com is merely an informational site about various aspects of ships operation,maintenance procedure, prevention of pollution and many safety guideline. The procedures explained here are only indicative, not exhaustive in nature and one must always be guided by practices of good seamanship. User feedback is important to update our database.For any comments or suggestions please Contact us
Other info pages !
Basic guideline for Container Ship Operation
Tanker vessel safety guideline Check items in oil tankers operation
Questions from user and feedback Read our knowledgebase
Cargo care at sea Precautions to be taken
Reefer cargo handling Troubleshoot and countermeasures
DG cargo handling Procedures & Guidelines
Cargo securing Check items prior departure port
Safe navigation Various factors affecting ships navigation at sea
Hull strength & stability Prior loading how to ensure hull strength & stability of ship
stevedores injury How to prevent injury onboard
Environmental issues How to prevent marine pollution
Safety in engine room Standard procedures
Site Map Page listing for this site.
Questions from user and feedback Read our knowledgebase
General precautions for tankers
General precautions prior entering freezing areas
Ship to ship transfer arrangement
Pumproom inspection for tankers
Transferring fuel oil onboard safety guideline
Inert gas system
Sounding of tanks and bilges
Oil pollution control method
Gas freeing arrangement for oil tanker
Handling guideline for oil cargo
Oil pollution prevention method
Preparation for loading oil cargo
How to prevent spillage of oil cargo
General precautions for oil cargo loading in tankers
General precautions for tankers
Related articles
Safety practice for crude oil washing onboard oil tankers
Oil tanker operations - tank cleaning,purging & gas freeing
Safety checks prior discharging sludge from ship to reception facilities
Bulk liquid cargo handling - Ship to shore safety checklist
Ship-to-ship transfer / Operational guideline and check item for oil tankers
General precautions for tankers
Safety precautions prior transferring oil
Reporting oil spillage in foreign ports
How to use low sulphur fuel oil onboard
Operational guideline during bunkering
Fuel oil sulpher quantity frquently asked questions
What is fuel oil additive ?
Guideline for Proper heating of Fuel Oil storage tank
Home page
|