Double hull tankers have traditionally been seen as endeavoring a higher level of oil
spill prevention comparing to single-hull construction. The exterior, double
hull of the vessel, can be infiltrated without causing a discharge of load. Several
studies have manifested that the oil outpouring rate from a double hull tanker
affected by a grounding or hull breach is usually less than that of other tanker
designs.
The practical event confirms these studies, as there have been a number
of occurrences where a double hull tanker's outer shell has been breached, but pollution
has been circumvented by the containment afforded by an individual intact inner hull.
However, a double hull does not limit an oil spill from occurring in and of itself.
Its prevention value lies in lessening spill size, or severity of the tanker does
encounter a hull breach or accident.
Oil spill statistics reveal that overall oil spillage degrees from tankers have been
on the downturn for the past few decades. Recent studies examining oil spillage rates
from tankers based on hull design suggest that double-hull tankers spill less
than pre-MARPOL single-hull tankers, double bottom tankers, and double-sided.
tankers. However, post-MARPOL single-hull tankers with segregated ballast tanks
seem to have similar spillage flows to double-hull tankers.
Overall, it is
difficult to make meaningful correlations between the declining fleet of non-double hull
tankers and the newer OPA 90 and MARPOL double-hull designs, because of relatively limited information. Additional studies may help define the
relationship between tanker hull configuration and oil spillage rates.
There remains to be some controversy regarding the overall prevention benefit of a
double hull oil tanker. A 2003 report published by the Oil Companies International
Marine Forum (OCIMF) warns that the complex design and structure of double-hull
tankers can make them more sensitive to sustaining and operations problems.
Like all vessels, double hull tankers can still be prone to catastrophic structural
collapses, particularly if they are not maintained and operated to high criteria.
Perhaps the most important consideration in evaluating the overall oil spill
prevention value of a double hull tanker design is the role of human factors – human
and organizational errors – in oil spills and tanker accidents. Research shows
that most crude oil tanker accidents involve the interplay between humans,
organizations, systems or equipment, oil spills, and accident prevention measures
that are often disproportionately focused on the engineering or technological "fixes," most easily remedied.
As the new classes of double-hull tankers that
transportation oil become increasingly reliant on engineered systems and automated technologies, the humans that operate these systems are subjected to new
challenges that may increase accident risks. Furthermore, while accident exposures with a
technological basis can often be remedied through engineering, human-technology interactions are much more difficult to address.
Double hulls are an essential component of the oil spill prevention system, but they are not
the only component.
A double hull does not in and of itself preclude an accident or
chain of events that could lead to an oil spill from occurring; it lessens oil spill risks
by reducing the amount of oil that might be released if an incident or accident should
occur. The only way to safeguard against the potential for future oil spills from
double-hull tankers is to create an efficient prevention system, including engineering and human factor components.
A recent study reveals that half of all major oil pollution claims arise from incidents on ships not carrying oil cargo. Although major spills receive international attention, they contribute to less than 5-10% of oil pollution reported. When oil spills into the aquatic environment, it can harm organisms that live on or around the water surface or under the water. Spilled oil can also damage parts of the food chain, including human food resources.
Although many species are harmed or killed soon after contact with the oil, other effects are not noticed immediately and can be longer-lasting:
- wildlife can be slowly poisoned by long term exposure to toxins
- predators can be exposed to oil by eating contaminated prey
- scientists have observed developmental effects in bird embryos that were exposed to oil
In 1973, IMO adopted the International Convention on Prevention of Pollution from Ships, now recognized globally as MARPOL, which has been amended by the Protocols of 1978 and 1997 and kept refreshed with important amendments. The MARPOL Convention inscribes pollution from ships by oil; by noxious liquid substances carried in bulk; harmful substances carried by sea in packaged form; sewage, garbage, and the prevention of air pollution from ships. Preventing oil spillage from a tanker there involved many complexities. Routine shipboard operations that are of greater concern have explained below:
- bilge water disposal
- tank washing
- ballasting
- fuel transfer
- loading / unloading cargo on tankers.
MARPOL 73/78 Annex I:
- Discharges of oil are permitted within limits considered 'reasonable and practical.' These limits are set out clearly in MARPOL Annex I.
- According to MARPOL Annex I, oil discharge is prohibited in 'special areas' (with minor exceptions) i.e. areas which are extremely vulnerable to oil pollution.
As part of the environmental policy, regulations in MARPOL Annex I have to be considered during ballast operations. It is to ensure that ballast water is not contaminated by oil products due to failures e.g., failure of bulkheads/joints between tanks or pipework systems that run through ballast tanks.
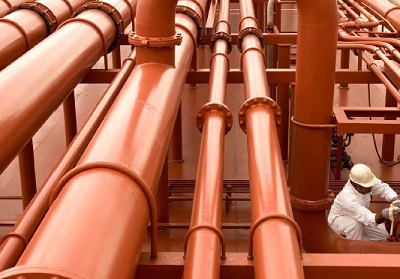
Well maintained pipeline
Ballast overboard discharge valves are to be kept closed and warning notices posted at the valves, engine and cargo control rooms before the vessel enters port or designated Special Areas.
Any discharge into the sea of oil or oily mixtures from the cargo area of an oil tanker shall be prohibited, except when all the following conditions are satisfied:
- the tanker is not in a Special Area
- the tanker is more than 50 nautical miles from the nearest land
- the tanker is proceeding en route
- the rate of discharge does not exceed 30 litres per nautical mile
- the total quantity of oil discharged does not exceed 1/30,000 of the total quantity of the cargo
- the tanker has an Oil Discharge Monitoring Equipment(ODME) in operation.
The discharged monitoring and control system should be used to release residue (Regulation 15).
Tanker Standard Equipment For Disposal Of Spilled Oil & Secondary Disaster Prevention
Slop Dump (Surface) Valve Arrangement (Emergency drains)
The slop dump valve arrangement is generally provided at the aftermost portion of the tank deck area. It connects the "On-Deck" accumulation to the slop tank(s) on either side of the ship (where fitted).
Opening of the drain valves in the case of an on-deck oil spill must be authorized by the Chief Officer, or in his absence, the duty deck officer. Close attention must be taken of positive pressure in the slop tank; correct draining procedures must be followed.
A warning sign, displayed well above such fish plate level, with the text "Not to be opened without authorization from the Chief Officer or the duty deck officer" should be posted by the drain valves.
Every Quarter, the functional testing of the Slop Tank Dump (Surface) Valves is to be exercised using "Quarterly Testing Record for Miscellaneous Equipment"
During drills, the crew must be properly instructed on the correct draining procedures to be followed at each case of an oil spill. Incorrect procedures could lead to serious aggravation of the case.
Equipment and Materials for on deck Oil Spill Clean up
The company designates Equipment and Materials for on deck Oil Spill Clean up in "Shipboard Oil Pollution Emergency Plan (SOPEP)."
Vessel's equipment for clean up of an 'on deck' oil spill shall be distributed correctly to prepare for Emergency Measures. Steel Drums should not be directly placed or moved on deck without suitable non-conductive insulation beneath.
The Portable Pneumatic Diaphragm Pump shall be ready to use at aft Main deck.
And Stripper pump (during discharge operations only) should be kept in a state of readiness for the intended duration of operations.
Refer to onboard SOPEP manual (or CFR 33 part 155.205 or 155.210 as applicable if in US navigable waters).
Emergency Procedures - Incident at Manifold/Tank Overflow
The cargo manifold constitutes a high-risk area. Accidents occurring in this area may be divided into two types:
i) Spillage through a fractured pipe or other cause that has not resulted in a fire.
ii) A spillage that has resulted in a fire.
In either case, the first consideration will be to cut off the supply to the area. If the ship is discharging, this can only be done by stopping the ship's pumps and closing a valve between the pump and the fracture. If the ship is loading it will be necessary for the shore installation to stop the supply and the means of communication or special signals must be established before loading is commenced.
Concerning the emergency shutdown of operations before loading or discharging is commenced in such incidents the appropriate contingency plan must be activated.
The large surface area created by a typical spillage will allow the oil to give off gas more rapidly than would normally be the case. If a source of ignition is present, the resulting fire could create a major conflagration beyond the extinguishing ability of the emergency party.
The Chief Officer must ensure that all possible ignition sources are isolated or removed. The spillage area is to be covered with foam to minimize the risk as soon as possible before cleaning up operations are commenced. Careful judgment must be exercised as this action could spread the oil further causing greater risk and serious environmental pollution.
Under these circumstances, spillage of oil or tank overflow will be considered as an emergency, and the Emergency Organisation brought into operation.
Inert Gas System
Main purpose of Inert Gas System is:
Maintain Pressure in Cargo Oil Tanks in proper range
Maintain Atmosphere in Cargo Oil Tanks as Inflammable Condition
In principle, all operations should be suspended if an Oil Pollution Incident occurs during Oil Transfer Operation. However, Inert Gas System may be operated continuously to prevent secondary disasters, Fire accidents.
How to Report an Emergency
The Master shall ensure that company’s internal and local emergency contact details are posted in public areas and in accordance with the “Shipboard Oil Pollution Emergency Plan”, the “Emergency Procedures for Oil pollution Accidents” and “Vessel Response Plan (VRP)” for the vessels to serve in U.S. water.
Static Electricity Precautions
An equal number of positive and negative ions, and under normal conditions is electrically neutral. It is true of oils, chemical products, and other liquids. A redistribution of ions tends to occur when a liquid comes into contact with a solid, giving rise to the formation of an Electric Double Layer. The ions adjacent to a liquid/solid interface are redistributed to produce a layer of ions of the same electrical sign. Slightly away from the interface, a layer of ions of the opposite sign will be formed. Elsewhere the distribution of ions remains unchanged.
When liquid and solid are separated, as in any pipeline flow, the ions in contact with the solid (pipe) tend to remain attached to the solid. The oil (or other liquid) loses some of its ions, thus becoming electrostatically charged. The separated charges will attempt to recombine, their success depending upon the electrical conductivity of the oil. Crude oils, which contain high levels of impurities, have high electrical conductivity and rapid charge recombination. Water also has high electrical conductivity.
By comparison, most refined products (white oils) contain few impurities, and charge recombination in such products is very slow. These products are known as STATIC ACCUMULATOR OILS.
The flow rate through pipes will influence the build-up of charge separation - the faster the flow, the faster the charge separation.
Charge separation will also occur:
- In the filling lines of tanks being loaded with white oils.
- When oil mixes with water.
- When air is allowed to "bubble" through white oils and splashing occurs at the surface.
- When oil is splashed or sprayed.
- When water droplets in a steam jet (or CO2 particles) leave a nozzle.
- When water passes through tank cleaning machines at high-pressure, electrostatic charging of fine sprays or mists may result.
Click here for a list of Static Accumulator Cargoes.
Related articles:
Basic procedure for pumproom management
Ship to ship transferring oil Basic procedure and guideline
Oil pollution control Oil tanker safety guideline
Oil pollution countermeasures Oil tanker safety guideline
Oil cargo loading Preparation and guideline
Oil spillage prevention Oil tanker safety guideline
Disaster prevention in oil tanker Procedure and guideline
Acceptance / rejection of fuel in a quality dispute
Operational guideline during bunkering
Bunker fuel sulfer limit of 3.50 % - Fuel Oil Regulations Frequently asked questions
Ships bunkering guideline- planning, preparation, safety checks & confirmation
Bunkering arrangement and safety factors onboard
Bunkering safe procedure and detail guideline for ships
How to keep bunkering record ?
Precautions prior transferring fuel oil into storage tanks
Treatment of waste oil and oily bilge
Bulk liquid cargo handling - Ship to shore safety checklist
Procedure for oil tankers and how to maintain records
Acceptance or rejection of fuel oil
Heating of fuel oil storage tank
Fuel oil viscosity control
Ships bunkering guideline- planning, preparation, safety checks & confirmation
Tanker vessel safety guideline - inert gas system
Tanker vessel safety guideline - gas freeing procedure
Precautions prior entering freezing zone - Check items in oil tankers operation
Tanker vessel safety guideline Check items in oil tankers operation
Tanker vessel safety guideline - how to prevent oil spillage
Tanker vessel safety guideline - tank cleaning procedures
How to ensure safe working atmosphere onboard?
Related Information
General guidance for oil tankers
Tanker equipment and machinery
Pumproom procedure
Pumproom inspection for tankers
Treatment for waste oil or oily bilges
Oil pollution prevention method
General precautions for tankers
Tanker equipment and machinery
General guidance for oil tankers
Crude oil washing for tankers

Other info pages !
Ships Charterparties Related terms & guideline
Stevedores injury How to prevent injury onboard
Environmental issues How to prevent marine pollution
Cargo & Ballast Handling Safety Guideline
Reefer cargo handling Troubleshoot and countermeasures
DG cargo handling Procedures & Guidelines
Safety in engine room Standard procedures
Questions from user and feedback Read our knowledgebase
Home page

ShipsBusiness.com is merely an informational site about various aspects of ships operation,maintenance procedure,
prevention of pollution and many safety guideline. The procedures explained here are only indicative,
not exhaustive in nature and one must always be guided by practices of good seamanship.
User feedback is
important to update our database. For any comment or suggestions please Contact us
Site Use and Privacy - Read our privacy policy and site use information.
//Home //Terms and conditions of use
Copyright © 2015 www.shipsbusiness.com All rights reserved.
